Original title: What does the equipment management information system of lean barrel manufacturing (358) include?
Q
What does the equipment management information system include?
A
Different enterprises and different equipment management modes have their own characteristics in the development of equipment management information systems, but their basic functions and methods are consistent. Generally, it includes equipment pre management system, fixed assets management system, equipment file management system, equipment maintenance management system, equipment operation management system, equipment spare parts management system, equipment maintenance management system, etc.
Detailed answers

Development of equipment management information system for different enterprises and different equipment management modes They have their own characteristics, but their basic functions and methods are consistent.
1. Equipment pre management subsystem
Equipment pre management is the beginning of equipment life cycle, including equipment planning, bidding and selection Type decision and design Standby design and manufacturing, installation acceptance, contract management, initial management of equipment use Etc. The basic file of equipment and the basic number of fixed assets management shall be formed in the early stage management of equipment According to. Its function module is shown in Figure 1.

Figure 1 Functional module diagram of equipment early stage management subsystem
The database data structure is as follows:
1) Equipment number, name, model, specification, equipment category , drawing number, weight Overall dimension, design unit, manufacturing unit, ex factory date, ex factory number.
2) Spare part number, spare part name, model, specification, drawing number, unit weight, installed capacity Manufacturer and spare parts category.
3) Installation unit, required installation technical parameters, actual installation technical parameters, special equipment Standby license number.
4) Information related to bidding.
5) Evaluation elements and relevant information of equipment selection decision.
6) Acceptance criteria and actual acceptance data.
7) Contract number, supplier name, contract signing time, delivery time, quantity Unit price, technical parameters, performance, delivery place and remarks.
8) Attachment number, name, model, specification, drawing number, quantity, etc.
The database data structure content and system function of the equipment pre management subsystem focus on management Technical data that may affect the equipment after it is put into use cannot include equipment design, manufacturing The whole process management of construction shall be formulated by different enterprises according to their own characteristics.
2. Fixed assets management subsystem
Fixed asset management includes fixed asset registration, scrap, usage status, transfer, and discount Used, leased, etc. The data related to fixed asset registration comes from equipment early management, and its functions The module is shown in Figure 2.

Figure 2 Functional module diagram of fixed assets management subsystem
The database data structure is as follows:
1) Fixed asset number, name, model, specification, asset category, drawing number, weight Overall dimension, manufacturer, ex factory date, date of use, ex factory number, original value Present value, annual depreciation rate, depreciation life, use status and use unit.
2) Lease in company, lease out company, lease term, lease price, payment method, lease contract Same as.
3) Number of special equipment use permit, time of last annual inspection and time of next annual inspection.
4) Attachment number, name, model, specification, drawing number, quantity, etc.
3. Equipment file management subsystem
Equipment archives management includes basic equipment archives, equipment drawings, and equipment operation files Case, equipment maintenance file, equipment repair file management, etc. The basic equipment file data comes from Equipment pre management; Equipment operation file data comes from equipment operation management; Equipment maintenance file Case data comes from equipment maintenance management; The equipment repair file data comes from the equipment repair management Li. Its function module is as shown in the figure 3.

Figure 3 Function module diagram of equipment file management subsystem
The data structure of the equipment drawing data management database is as follows: equipment number, equipment name call , drawing number, drawing, storage location, drawing status, lending, borrower, borrowing time Time, estimated return time, return time, remarks, etc.
4. Equipment maintenance management subsystem
Equipment maintenance management includes equipment lubrication management and equipment spot check management. Equipment maintenance pipe Reason should be formed Equipment maintenance files provide equipment maintenance basis for equipment maintenance management Operation management provides assurance and obtains requirements for equipment maintenance from operation management. Its function module As shown in Figure 4.
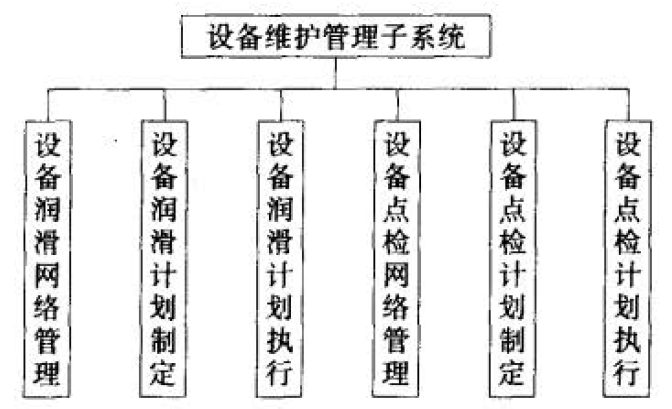
Figure 4 Functional module diagram of equipment maintenance management subsystem
The database data structure is as follows:
1) Equipment number, equipment name, drawing number, factory number, use status, use list Position, lubrication point distribution diagram, point inspection point distribution diagram, lubrication responsible person, point inspection responsible person.
2) Lubrication point number, lubricant name, manufacturer, additive name, lubrication week Period, refueling volume, refueling time, next refueling time, lubrication condition evaluation, equipment condition evaluation Estimation.
3) Point inspection number, point inspection cycle, instruments and equipment used for point inspection, point inspection time Time of next point inspection, existing problems, handling opinions, required handling time, handling results, handling Time, processing unit, executor, etc.
Some enterprises also carry out cleaning, spot inspection and maintenance (fastening, plugging, adjustment, anti-corrosion Vibration, centering) and lubrication are integrated into one, which is called standardized operation of equipment maintenance System, make corresponding changes to the above system modules.
5. Equipment operation management subsystem
Equipment operation management refers to various data and parameters (such as temperature, pressure Force, vibration, etc.), equipment start time, failure time, etc. Equipment transportation Line management should form equipment operation files. Its function The module is shown in Figure 5.

Figure 5 Functional module diagram of equipment operation management subsystem
The database data structure is as follows:
1) Equipment number, equipment name, drawing number Factory number, use status, user, transportation Line parameter monitoring point distribution diagram, equipment management responsibility Person in charge of equipment operation.
2) Parameter monitoring point number and monitoring item name Scale, unit, standard good value, alarm value, record Record time, record value and equipment operation status evaluation.
3) Start date and time of equipment downtime, end date and time of equipment downtime, and downtime (minutes), reasons for shutdown, and brief description of reasons.
4) Statistical time, equipment availability, equipment availability, etc.
6. Equipment spare parts management subsystem
Equipment spare parts management is the most important subsystem of equipment management information system. Application equipment ABC classification management, quota management, fixed location management, collaborative inventory and zero inventory of spare parts Management and other means to ensure the normal production and economic efficiency of the enterprise. Its functional modules are as follows Figure 6.

Figure 6 Functional module diagram of equipment spare parts management subsystem
The database data structure is as follows:
1) Equipment number, name, model, specification, equipment category, drawing number, weight Dimensions and manufacturing units.
2) Spare part number, spare part attribute number, spare part name, model, specification, drawing number Material, unit weight, installed capacity, service life, approved annual consumption, processing and ordering cycle Low reserve quota, maximum reserve quota, spare parts category.
3) Plan No., Planned Ordering Quantity, Planned Ordering Time, Planner, Planner Bit.
4) Supplier No., name, address, postal code, contact number Contact person, deposit bank, account number, legal representative, rating grade.
5) Contract number, manufacturer's contract number, contract signing quantity, contract unit price, additional Fees, freight and miscellaneous charges, advance payment amount, quality assurance amount, quality assurance time, delivery time, transporter Type, delivery place, settlement method, contract signing date, purchaser.
6) Contract settlement quantity, settlement unit price, settlement surcharge, settlement freight and miscellaneous charges, settlement Total price, invoice number, dishonor amount, dishonor reason.
7) Borrower, loan date, loan amount, offset date, and offset amount.
8) Warehousing number, warehousing time, warehousing quantity, warehouse keeper, and delivery data.
9) Inventory quantity, inventory unit price, storage location and remarks.
10) Collecting No., Collecting Time, Fund Source, Collecting Quantity, Issue Unit Price, Collecting Employer, receiver, etc.
Spare parts management and general merchandise purchase, sales and inventory management have both similarities and characteristics. it It serves production. The purpose of collaborative inventory and zero inventory management is to reduce inventory. prepare The purpose of piece coding is to quickly query and count the types of spare parts for each piece of equipment How many pieces of equipment are used? Therefore, a dual coding rule of spare part code and spare part attribute code is proposed Then. The spare parts coding rule is based on the place of use of spare parts; The coding rule of spare parts attribute is It is coded according to the attribute of spare parts, which does not involve the place of use of spare parts.
7. Equipment maintenance management subsystem
Equipment repair management includes equipment repair plan management, material management, and equipment repair execution Management and equipment maintenance quality management. Equipment repair management should form an equipment repair file. his The function module is shown in Figure 7.

Figure 7 Functional module diagram of equipment maintenance management subsystem
The database data structure is as follows:
1) Equipment number, name, model, specification, equipment category, drawing number and equipment introduction.
2) Maintenance plan number, maintenance project name, maintenance nature, and when maintenance is required Time, estimated construction period, maintenance content, cooperation requirements, maintenance unit, user unit responsible person Person in charge of maintenance.
3) Number, name, model, specification, drawing number, quantity and unit price of spare parts required.
4) Required material number, material name, material model, material specification, material quantity Material unit price, material category, unit, unit weight and storage location.
5) Name of required type of work, man hour, unit price of man hour, name of required equipment, equipment model Equipment specification and quantity.
6) Actual maintenance start time, actual maintenance content, actual use duration, test run Vehicle technical data and maintenance summary.
7) Number, name, model, specification, drawing number and quantity of spare parts actually used.
8) Actual material number, material name, material model, material specification, material Quantity and receiver.
9) Name of actually used work type, working hours, name of actually used equipment, equipment model Equipment specification and quantity.
10) Maintenance contract number, settlement of labor costs, settlement of spare parts costs, settlement of material costs Use, settlement of equipment costs, settlement of other costs, settlement of total costs and settlement time, etc.
11) Equipment acceptance quality standards, inspection precision points, acceptance record forms, acceptance confirmation Reports, etc.
8. Features of equipment management information system
(1) Coding consistency
Equipment management information system equipment code runs through all subsystems, and links all subsystems Tie it up 。 The equipment code is further expanded into fixed asset code and equipment spare part code.
(2) Variable length polyface code for spare part attribute code and material code
Spare part attribute code and material code are based on the inherent characteristics of equipment spare parts and materials It is impossible to code all spare parts and materials of equipment used at one time Code must be continuously supplemented according to the continuous increase of equipment and materials used. can The variable length coding method allows the capacity of coding and the content expressed to be continuously extended, while And a data item may have multiple characteristics.
(3) Data sharing
Each subsystem of the equipment management information system is an independent system, but It is connected by equipment code. In order to reduce the workload of data input and data output Wrong opportunity. One kind of data should have only one population, which becomes the shared number of the management system According to. Go back to Sohu to see more
Editor in charge: